Artificial intelligence detects defects in wind turbines before they become problematic
It is a costly endeavour to inspect, avoid or repair defects in wind turbines – but left unattended a defect could lead to catastrophic failure. The middle road exists, but finding it can be hard. Wind Power LAB uses AI as their pathfinder to strike the perfect balance between costs and catastrophe.
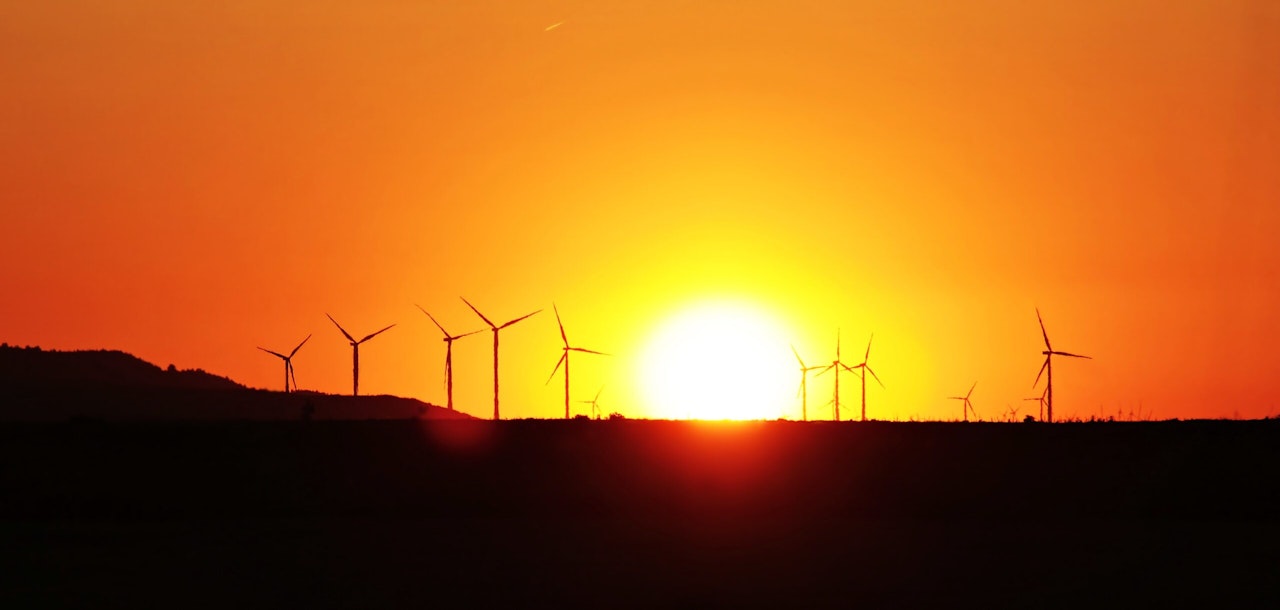
Leaving things unattended has a price, but so does being overly cautious. Generally, when it comes to wind turbines, it is difficult to understand whether a defect will worsen – or if a repair is a prudent solution.
“As we transition to green energy, we increasingly need to trust that our wind turbines and solar panels are working as they should. Some defects are easy to detect. But our speciality is finding the silent defects. The ones that don’t show up on a sensor, so you have to check with a drone or similar to detect them,” Anders Røpke, the CEO of Wind Power LAB, says.
Wind Power LAB has carved out a niche so tight that today they serve a global client base. Furthermore, wind turbines have become a central player in many countries’ energy strategies. A role that will likely continue to increase as the world is expected to increase its reliance on the technology. As the number of turbines increase so does the need for maintenance.
Focused on costs
For the past few years, many wind turbine owners have been moving away from annual routine checks and are increasingly looking at operating with fixed schedules for what defects to fix and when, as well as calculating the cost.
“You can compare it to humans going to a dentist. We want to know about problems before they become an issue, so we can get them fixed. In the same way, defects to wind turbines can develop and turn so serious that they become too expensive to fix. They can occur from lightning, rain or just wear and tear, what’s called leading edge erosion. These are issues you want to fix at the right time to avoid affecting your investment,” Anders Røpke underlines.
Wind Power LAB solves this task using AI that is trained to recognise and analyse defects in wind turbines. Typically, these types of issues can be difficult to spot with the naked eye. Therefore, it requires deep industry knowledge combined with careful analysis to decide whether the defects needs repairing.
Calculations, computations and counselling
A typical job consists of analysing images of a wind turbine taken by a drone pilot, for instance. These images are analysed in the cloud by artificial intelligence technology, which has been developed by Wind Power LAB and trained to find defects which may not be visible to the human eye.
What is unique about the company’s product is that its report on the condition of a wind turbine also includes recommendations across a number of variables. For instance assessing whether the cost of fixing defects and the timeframe for doing so relative to the position of the wind turbine. Not all defects become serious issues. Often, this will depend on the position of the wind turbine and the load it takes over time.
Using these insights, the wind turbine owner can then decide when it makes sense to fix a defect.
“We sometimes see wind turbine blades with damage exceeding costs of 50,000 Danish kroner. It could be the wind eroding the blade or a lightning strike that charred the blade inside without it being visible. But it could also be wind, rain drops and ice sandblasting the blades. It’s a complex issue to work out, and there are many scenarios out there,” he says.
These scenarios vary from owners wanting to minimise operating costs as much as possible, to technicians earning a living from repairing defects and therefore preferring repairs to be as extensive as possible. The justification here is being able to help show what that calculation actually looks like.
“This is precisely what we can do. While the image analysis could, strictly speaking, be made manually in Bangladesh, it’s the balance between AI and human expertise that creates value,” Anders Røpke says.
The highly specialised company also has various ideas for future growth areas. One option that Anders Røpke is keeping an eye on is whether it might be possible to send autonomous drones to check for defects without requiring a pilot to steer them.
Wind Power LAB already offers a service for uploading images of possible defects which are then analysed within 24 hours and sent back along with recommendations on when to repair a defect in relation to the cost.
The company was founded in 2016 and has had funding from several investors, including Innovation Fund Denmark.